Revamp Your Workflow: Unleashing Excellence in Product Manufacturing
In today’s fast-paced industrial landscape, the competition is fierce, and manufacturers must continually seek ways to enhance their operations. The secret to standing out lies in optimizing production processes and adopting innovative techniques that lead to exceptional product manufacturing. As businesses strive to meet escalating customer demands while maintaining high standards, revamping workflow becomes essential.
Embracing a holistic approach to product manufacturing not only boosts efficiency but also fosters a culture of excellence within the organization. By focusing on the integration of advanced technologies and streamlined processes, manufacturers can unleash the full potential of their workforce and resources. This article explores the transformative strategies that can elevate your production capabilities and drive sustainable growth in your business.
Streamlining Production Processes
Efficiency is key in product manufacturing , and streamlining production processes can significantly enhance productivity. Start by analyzing each step in your current workflow to identify bottlenecks and redundancies. Implementing lean manufacturing principles can help eliminate waste and optimize the use of resources. By focusing on continuous improvement and regularly reviewing processes, manufacturers can create a more agile environment that adapts to changing demands.
Automation plays a crucial role in modernizing production lines. By integrating advanced technologies such as robotics and AI-driven systems, manufacturers can increase precision and speed while reducing the chances of human error. Automated solutions not only improve output but also free up skilled workers to focus on higher-value tasks, fostering innovation within the organization. Investing in the right automation tools can lead to significant long-term savings and efficiency gains.
Collaboration among teams is essential for a seamless manufacturing process. Encouraging open communication between engineering, production, and quality assurance can help identify issues early and drive faster resolutions. Utilizing collaborative tools and software can enhance visibility across departments, allowing for real-time tracking of progress and providing insights into potential improvements. By fostering a culture of teamwork and shared responsibility, organizations can create a more cohesive and streamlined workflow that drives excellence in product manufacturing.
Implementing Advanced Technologies
In the fast-paced world of product manufacturing, integrating advanced technologies is crucial to optimizing production processes. Automation tools, such as robotic arms and intelligent conveyor systems, can significantly enhance efficiency and reduce labor costs. By leveraging these technologies, manufacturers can streamline operations, improve precision, and minimize human error, resulting in higher quality outputs. The adoption of artificial intelligence and machine learning also allows for data-driven decision-making, enabling companies to predict maintenance issues and optimize resource allocation.
Another key advancement is the use of the Internet of Things (IoT) in product manufacturing. IoT devices enable real-time monitoring of machinery and equipment, providing valuable insights into performance and operational efficiency. This connectivity allows manufacturers to identify bottlenecks in the production line, assess machine health, and implement preventive measures to avoid downtime. When manufacturers harness the power of connected devices, they can create a more responsive and agile production environment that adapts quickly to changes in demand.
Finally, implementing advanced manufacturing technologies like 3D printing can revolutionize the way products are designed and produced. This additive manufacturing technique allows for rapid prototyping and the creation of complex geometries that traditional methods struggle to achieve. It not only reduces material waste but also accelerates the time-to-market for new products. By investing in such innovative technologies, manufacturers can enhance their creativity and efficiency, ultimately leading to a competitive edge in the market.
Measuring Success and Continuous Improvement
In the realm of product manufacturing, measuring success hinges on clearly defined key performance indicators. Metrics such as production efficiency, product quality, and customer satisfaction play a pivotal role in evaluating the effectiveness of manufacturing processes. Tools like Six Sigma and lean management can be employed to provide a structured approach to identify areas for improvement and ensure that the manufacturing team is not only meeting but exceeding set targets. By consistently monitoring these indicators, manufacturers can gain valuable insights into their performance and make informed decisions.
Continuous improvement is essential for staying competitive in the ever-evolving market landscape. It involves a systematic approach to enhancing processes, products, and services. Engaging employees at all levels to contribute ideas fosters a culture of innovation and accountability. Techniques such as regular feedback loops and performance reviews can help ensure that improvement initiatives are aligned with business objectives, enabling organizations to adapt swiftly to changes and respond proactively to customer needs.
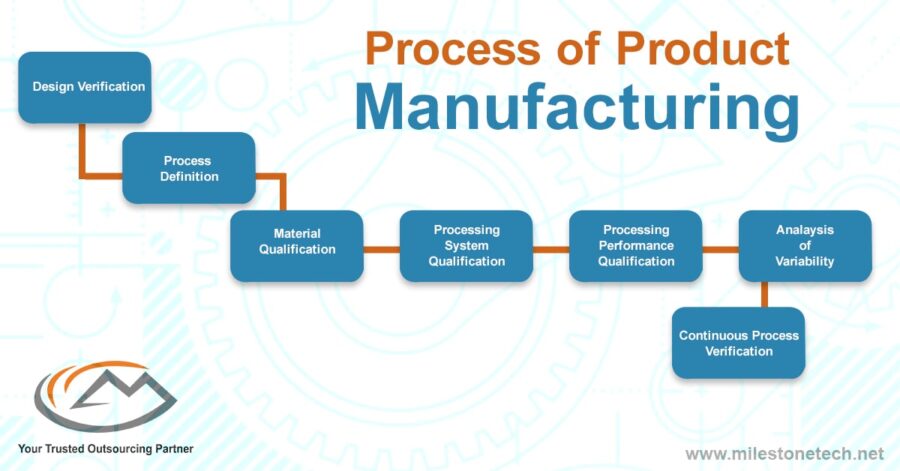
Ultimately, the journey of product manufacturing does not end with achieving initial success; it is an ongoing process. Organizations committed to excellence recognize that the landscape is always changing, and there is always room for growth. By embracing a mindset geared towards continuous improvement, manufacturers can not only optimize their current workflows but also pave the way for sustainable success in the future, ensuring they remain leaders in the industry.